The development and manufacture of a vehicle is becoming progressively more complicated and expensive. One of the most recent challenges is autonomous and electric vehicle platforms. They introduced a set of technologies and interfaces, such as semi-active and active suspension subsystems.
Not to mention manufacturers are always under pressure to cut costs and get products out faster. The global competition, loss of experienced workers, and changing testing methods make it even harder.
To solve vehicle development challenges efficiently manufacturers turn to cutting-edge technology. They combine an Electromagnetic Actuated Damper Test System with hardware-in-the-loop (HIL) testing.
In this blog post, we’ll dive into vehicle suspension HIL testing. We’ll cover its benefits, challenges, and how electromagnetic actuators play a key role in this advanced testing.
- What is Hardware-in-the-Loop (HIL) Testing?
- Vehicle Suspension HIL Testing Setup
- The Benefits of Vehicle Suspension HIL Testing
- The Role of Electromagnetic Actuators
- Considerations in Suspension HIL Testing
What is Hardware-in-the-Loop (HIL) Testing?
HIL testing is a simulation-based approach to develop and validate complex systems, such as vehicle suspension systems.
In simple terms, engineers take real-life suspension parts and connect them to a computer simulation. This lets them test and check how the suspension system would work, without actually having to build a whole new car just for testing.
So, instead of testing with a real vehicle, manufacturers can use a virtual vehicle model. That connects to a physical loading rig to simulate vehicle systems. This setup is ideal to test and develop suspensions and damping systems.
The primary advantage of HIL testing is the ability to simulate a wide range of operating conditions and scenarios. To achieve them in the real world would be difficult, expensive, or even dangerous to replicate.
This includes scenarios such as extreme weather conditions, road surface unevenness, and even unexpected vehicle maneuvers.
Vehicle Suspension HIL Testing Setup
In the realm of vehicle suspension systems, HIL testing has become an essential tool for manufacturers.
By combining the physical suspension components with a virtual environment, they can accurately simulate the behavior of the suspension system under various driving conditions. Such as maneuver-based evaluations, damper algorithm development, and traditional damper assessment.
To provide a comprehensive evaluation environment, the HIL testing setup for vehicle suspension typically includes the following key components:
- The physical suspension components, such as shock absorbers, springs, and control arms, are integrated into the HIL test setup.
- Electromagnetic actuators apply the necessary forces and displacements to the suspension components, simulating the real-world conditions, forces, and movements the suspension would experience.
- A comprehensive virtual simulation environment, often powered by advanced software, models the vehicle’s dynamics, road conditions, and other relevant factors.
- Sensors in the HIL setup measure the performance of the suspension components, providing valuable data for optimization.
The Benefits of Vehicle Suspension HIL Testing
By utilizing HIL testing for vehicle suspension systems, engineers can enjoy several key benefits:
- HIL testing lets engineers quickly test and improve suspension systems. They can make changes to either the virtual simulation or the real parts without having to build a full physical car each time. That is just too time-consuming.
- It is significantly more cost effective than traditional physical testing methods. It eliminates the need for building and testing multiple physical prototypes.
- Engineers use this testing method to simulate real driving conditions and get the suspension ready for actual cars.
- Engineers can push the suspension to its limits safely using a computer setup. They don’t have to worry about breaking real parts or causing crashes.
In short, the system speeds up development by providing more realistic testing environments early in the process. This reduces the need for physical prototypes, track time, and other resources.
The Role of Electromagnetic Actuators
Electromagnetic actuators are crucial in making HIL testing for vehicle suspension work. These advanced devices can accurately mimic the forces and movements a suspension system would face during real driving.
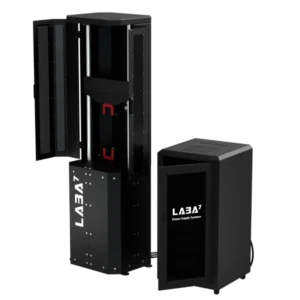
Here are a few key advantages of electromagnetic actuators in HIL testing:
- They can control the forces and movements acting on the suspension parts precisely. This lets them accurately simulate what the suspension would experience in the real world.
- Engineers can easily integrate electromagnetic actuators into the HIL test rigs. Then programs run simulations of a wide range of driving conditions and test how the suspension system behaves.
- Generally, electromagnetic actuators can withstand long and rigorous testing for extended periods, minimizing downtime and maintenance requirements.
- They have high-speed response and high bandwidth. These qualities allow the simulation of even the most dynamic and rapidly changing driving conditions. Engineers need it to thoroughly test the suspension system.
- Engineers can easily scale electromagnetic actuators up or down to fit different suspension systems and meet various testing needs. This makes them a versatile solution for a wide range of vehicle applications.
By leveraging the capabilities of electromagnetic actuators, manufacturers can enhance the accuracy and effectiveness of their vehicle suspension HIL testing. In turn, it will lead to the development of more advanced, reliable, and responsive suspensions.
Considerations in Suspension HIL Testing
While the benefits of vehicle suspension HIL testing are substantial, there are also several considerations that engineers must address:
- Ensuring the accuracy of the virtual simulation environment is critical. Any discrepancies between the simulation and the physical system can lead to inaccurate results. For example, faulty sensors can provide inconsistent data.
- Integrating the physical suspension components with the virtual simulation environment can be complex, requiring careful coordination and attention to detail.
Overcoming these challenges requires an integrated approach that combines expertise in multiple areas. For example, vehicle dynamics, control systems, and data analysis.
Conclusion
HIL testing, coupled with the capabilities of electromagnetic actuators, has become a crucial tool in the development and optimization of suspension systems. The tandem allows engineers to design and validate suspension systems more reliably, responsively, and efficiently.
As the car industry keeps changing, HIL testing with electromagnetic actuators will become even more important. When engineers and researchers use these technologies, they can make suspension systems work better than ever before. This helps create vehicles that are safer, more comfortable to ride in and use less fuel.
You also might like these articles:
- LABA7 Unveils New Specs for Electromagnetic Shock Dyno
- LABA7 EMA vs Alternatives
- EMA vs Other Shock Dynos of LABA7
- LABA7 Introduces Novel Power Supply System for Electromagnetic Shock Dyno
- Electromagnetic Linear Actuator vs Scotch-Yoke Shock Dyno: Which One To Choose?
- EMA Power Supply Unit Shortlisted for Innovation of the Year 2024